How Our SLS 3D Printing Service Works
Why Choose SLS Printing?
SLS printing offers several advantages that make it the preferred choice for engineers, manufacturers, and product designers.
High Strength & Durability
SLS printed parts are known for their excellent mechanical properties. These materials, such as PA11, PA12 and Carbon Fiber-reinforced composites, provide high impact resistance, making them ideal for functional prototypes and end-use applications.
No Support Structures Needed
Unlike SLA or FDM, SLS does not require support structures. This enables greater design freedom, allowing for complex geometries without additional post-processing to remove supports.
Material Versatility
3D printing SLS supports a wide range of materials, from flexible TPU for medical applications to high-stiffness Carbon Fiber PA12 used in aerospace and automotive industries.
Production-Ready Scalability
SLS 3D print is not just for prototyping—it is scalable for low-to-mid volume manufacturing, helping businesses reduce tooling costs and speed up production timelines.

Our SLS Printing Materials
We offer high-quality SLS 3D printing services, supporting both prototyping and production with a versatile selection of nylon printing materials. Whether you need strong functional parts or detailed visual models, our SLS 3D print solutions ensure durability and performance.

SLS 3D Printing Process
Selective Laser Sintering (SLS) is a powder-based 3D printing technology that uses a high-powered laser to fuse fine material particles layer by layer. This powder bed fusion process allows for the production of strong, durable, and complex parts without the need for support structures.
Here’s how the SLS process works:
Step 1 - Powder Distribution
A thin layer of polymer powder (PA12, PA11, TPU, or composite materials) is evenly spread across the build platform.
Step 2 - Laser Sintering
A laser selectively fuses the powder according to the digital model’s cross-section, solidifying the material where needed.
Step 3 - Layer Building
Once a layer is complete, a new layer of powder is applied, and the process repeats until the entire part is formed.
Step 4 - Cooling & Extraction
After printing, the entire powder bed needs to cool inside the machine to prevent warping. Once cooled, the finished parts are extracted from the unsintered powder.
Step 5 - Post-Processing
Parts are cleaned, excess powder is removed, and optional surface finishing techniques (such as bead blasting or dyeing) can be applied.
Examples of SLS Parts
See the quality and precision of our SLS 3D printed parts. This gallery highlights real components we’ve manufactured, from functional prototypes to production-ready parts.
Applications of SLS 3D Printing
Durable End-Use Parts
3D printing SLS is widely used for functional prototypes, automotive components, and industrial parts
Complex Geometries
Since no supports are needed, 3D print SLS is a great way to produce intricate, highly detailed structures
Diverse Materials
SLS printing services may be provided using PA12, PA11, TPU, or Carbon Fiber composites to match specific project's needs.
Low-Volume Production
SLS 3D printing is ideal for small production runs, reducing tooling costs.
How SLS Compares to Other 3D Printing Methods
Each 3D printing technology has its strengths, making it essential to choose the right method based on mechanical properties, material options, and design complexity. The table below provides a detailed comparison of SLS, SLA, and FDM.
Comparison Table
Feature | SLS 3D Printing | SLA 3D Printing | FDM 3D Printing |
---|---|---|---|
Support Structures | Not Required (Self-supporting powder bed) | Required (For overhangs & complex shapes) | Required (For stability during printing) |
Material Options | PA12, PA11, TPU, Carbon Fiber, PBT, PP, composites, flexible materials | Standard, tough, flexible, high-temperature resins | PLA, ABS, PETG, Nylon, Carbon Fiber, composites |
Strength & Durability | High (Tough, impact-resistant, suitable for functional parts & production runs) | Variable (Some resins are brittle, others can be tough but limited by UV sensitivity) | Moderate to High (Strong for functional parts, but layer adhesion can be a weak point) |
Surface Finish | Slightly grainy, matte (Can be smoothed with post-processing) | High-detail (Well-suited for visual models) | Layered texture (Visible layer lines) |
Best For | Functional prototypes, production-ready parts, complex geometries without supports | Visual models, complex designs | Affordable functional prototypes, technical parts where aesthetics are less critical |
Common Misconceptions About SLS Printing
Myth 1 - “SLS is too expensive”
Actually, while SLS may have a little bit higher upfront costs than FDM, it eliminates support structures and minimizes post-processing labor. It is highly cost-effective for complex, production-ready parts and reduces tooling costs for small-to-mid volume production.
Myth 2 - “SLS is only for prototyping”
SLS is widely used for end-use production parts in industries such as automotive, consumer products, and medical. It is scalable for manufacturing, not just prototyping. Many businesses leverage SLS for short-run production and bridge manufacturing, allowing them to bring products to market faster.
Myth 3 - “SLS prints are too porous”
While raw SLS prints have a slightly grainy texture, post-processing techniques such as bead blasting, dyeing, and polishing can produce smooth, sealed, and non-porous surfaces.
Myth 4 - “SLS printing lacks precision”
In fact, SLS achieves fine details with a layer resolution of 100μm, which is comparable to or better than many FDM prints and suitable for functional components requiring tight tolerances.
Post-Processing Options for SLS 3D Prints
Media Blasting
After printing, SLS parts typically go through a media blasting process. This step removes unsintered powder and gives the surface a more uniform, slightly smoother finish.
Polishing
Parts can be polished to further reduce surface roughness. Mechanical or chemical polishing techniques can be used to achieve a matte or semi-gloss appearance, depending on the application.
Dyeing & Painting
SLS prints, especially those made with PA12 or PA11, can be dyed for consistent color throughout the part. Alternatively, painting can be applied for customized finishes or aesthetic requirements.
Sealing & Coating
Sealants or specialty coatings may be applied to enhance properties like water resistance, UV stability, or chemical durability. This is especially useful for end-use parts in demanding environments.
Surface Machining
For parts requiring tight tolerances or mechanical fit, minor machining or tapping can be performed post-printing. This ensures proper assembly and function in technical applications.
SLS post-processing offers a versatile toolkit to improve both the functionality and appearance of your parts, making it suitable for a wide range of applications, from industrial tools to customer-facing products.
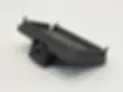
Why Choose Our SLS 3D Printing Services?
For businesses, engineers, and manufacturers looking for reliable and scalable 3D printing, our SLS 3D printing services deliver high-strength parts with excellent mechanical properties.
With over 12 years of experience, we’ve helped companies across industries create functional prototypes, durable end-use components, and complex geometries that wouldn’t be possible with traditional manufacturing.
We understand the importance of meeting deadlines. Our streamlined SLS 3D print process allows for production in as little as 2 business days, keeping your projects on schedule.
In-house Production
Diverse Materials
12+ Years of Experience
Lead Times from Two Days
Volume Discounts
Serving Boston businesses and
beyond
Get in Touch
We provide SLS 3D printing services in Salem, Greater Boston and throughout Massachusetts. We also ship nationwide.
Address: Enterprise Center at Salem State University, 121 Loring Avenue, Salem, MA 01970.
Meetings by appointment only.
Feel free to reach out to us via email at: sales@upsideparts.com, or by phone at: